I spent a couple of hours on Friday pouring over the recent invoices of my one-time partner Robin Gomm, who still runs the business, Complete Fabrications, that we started together in 1986. Cement prices up a little, block prices up a little, insulation prices up a lot, timber prices stable; no great surprises anywhere.
As I was leaving, Robin dipped into a filing cabinet and took out a pricing document that we used twenty years ago. It was handwritten, a document prepared in a pre-computer age, which made it seem somehow even more ancient than it actually was. It was fascinating to look at what had happened to costs over that timescale. You would instinctively feel that prices must have doubled, trebled or even quadrupled but what stood out were some items, notably plasterboard and timber products, which are actually cheaper today than they were in 1985. 12.5mm sheets of plasterboard were costing us over £4.00 a sheet back then: now Robin is paying £3.80.
Cement also made an interesting contrast. This most basic of building materials was costing £2.80 a bag back in 1985; currently the going rate seems to be £2.77. So is cement another example of inflation-free building costs? Unfortunately not. In the 1980s a bag of cement weighed 50kg. Now health and safety legislation prohibits the sale of bagged materials weighing more than 25kg so effectively cement has doubled in price as £2.77 buys you just 25kg. That’s equivalent to a 4% rise per annum and, coincidentally, equates exactly to the rise in the Retail Prices Index over that time period.
But cement stands out as one of the few building products that have actually kept place with inflation. My, admittedly subjective, reckoning has it that building materials as an amorphous grouping, have risen in price somewhere between zero and RPI. That is a trend which is likely to continue, higher energy costs notwithstanding. The main drivers behind increasing build costs are labour costs, which have risen more or less in line with house prices (i.e. far higher than RPI) and legislation, which requires us to put rather more into our houses today than we did in 1985.
The online ramblings of Housebuilder's Bible author Mark Brinkley. The paper version is updated every two years and is widely available via UK bookstores and Amazon
26 Sept 2005
22 Sept 2005
Building regs gather no Moss
After much delay, the Office of the Deputy Prime Minister has now published (on 13 Sep) the uprated regulations for energy efficiency (Part L) and ventilation (part F). Well, published draft versions, at any rate. If ever a cake was half-baked, this was it. That’s not to say that the proposals are batty: there is much good sense in them and they are obviously the result of a huge amount of work. It’s just that the energy efficiency measures don’t really seem to be all there yet.
New house designers, for instance, are referred to a website called www.modeldesigns.info where they can find details they can use in their fabric designs, in order to meet the new improved insulation standards. But click onto this site and what do you get? Just a page advertising low cost domain name registration and a note to say that this URL has been taken. At least the ODPM have registered the name! At least, we hope it's the ODPM. It could be Kate Moss looking for a new career. But whoever has it, it will presumably be some time before guidance is proffered.
The big issue that was getting everyone excited was testing for air tightness. Most commentators were agreed that there really wasn’t much point just tightening U values endlessly because without much higher building standards, the extra insulation wasn’t doing anything. However, universal pressure testing is impractical as there simply aren’t enough blower doors, or qualified testers, to go around. What seems to have emerged is a compromise. Developers building estates will be subjected to certain random tests. Of particular interest to selfbuilders and small developers is the option to avoid the need for any pressure testing by using a value of 15 m3/(h.m2) for the air permeability at 50 Pascals when undertaking the heat loss calculations. This is 50% higher than the air permeability standard being asked for on pressure-tested houses, so in effect there is a trade-off. You want to avoid the pressure test? Then you have to pack in more insulation.
But how much more? On that, Part L remains evasive. And presumably will continue to do so until such time as www.modeldesigns.info bursts into life.
In time, I suspect that the next Part L will bed in just fine and I am in the camp that thinks pressure testing will prove extremely useful in raising building standards, though it’s sure to raise all sorts of hackles in the short term.
But lurking in the new draft version of Part F, the ventilation regs, is a new requirement that I suspect may end up upsetting a large number of new homeowners. It states:
To ensure good transfer of air throughout the dwelling, there should be an undercut of minimum area 7,600 mm2 in all internal doors above the floor finish (equivalent to an undercut of 10 mm for a standard 760 mm width door).
There is logic to this. How can you ventilate a house properly if you seal off individual rooms from one another? And to be perfectly honest a 10mm gap isn’t really very much: much less than this and your bedroom doors will start binding. But there is something about being told that you have to have a 10mm undercut which I feel sure is bound to get people’s goat. Can you see it? Officious building inspector going around checking the undercut on your doors? You really wonder why they have bothered to add this clause, unless it’s the thin end of the wedge and the next revision of Part F will ask for 25mm. Yikes.
New house designers, for instance, are referred to a website called www.modeldesigns.info where they can find details they can use in their fabric designs, in order to meet the new improved insulation standards. But click onto this site and what do you get? Just a page advertising low cost domain name registration and a note to say that this URL has been taken. At least the ODPM have registered the name! At least, we hope it's the ODPM. It could be Kate Moss looking for a new career. But whoever has it, it will presumably be some time before guidance is proffered.

The big issue that was getting everyone excited was testing for air tightness. Most commentators were agreed that there really wasn’t much point just tightening U values endlessly because without much higher building standards, the extra insulation wasn’t doing anything. However, universal pressure testing is impractical as there simply aren’t enough blower doors, or qualified testers, to go around. What seems to have emerged is a compromise. Developers building estates will be subjected to certain random tests. Of particular interest to selfbuilders and small developers is the option to avoid the need for any pressure testing by using a value of 15 m3/(h.m2) for the air permeability at 50 Pascals when undertaking the heat loss calculations. This is 50% higher than the air permeability standard being asked for on pressure-tested houses, so in effect there is a trade-off. You want to avoid the pressure test? Then you have to pack in more insulation.
But how much more? On that, Part L remains evasive. And presumably will continue to do so until such time as www.modeldesigns.info bursts into life.
In time, I suspect that the next Part L will bed in just fine and I am in the camp that thinks pressure testing will prove extremely useful in raising building standards, though it’s sure to raise all sorts of hackles in the short term.
But lurking in the new draft version of Part F, the ventilation regs, is a new requirement that I suspect may end up upsetting a large number of new homeowners. It states:
To ensure good transfer of air throughout the dwelling, there should be an undercut of minimum area 7,600 mm2 in all internal doors above the floor finish (equivalent to an undercut of 10 mm for a standard 760 mm width door).
There is logic to this. How can you ventilate a house properly if you seal off individual rooms from one another? And to be perfectly honest a 10mm gap isn’t really very much: much less than this and your bedroom doors will start binding. But there is something about being told that you have to have a 10mm undercut which I feel sure is bound to get people’s goat. Can you see it? Officious building inspector going around checking the undercut on your doors? You really wonder why they have bothered to add this clause, unless it’s the thin end of the wedge and the next revision of Part F will ask for 25mm. Yikes.
16 Sept 2005
Do building regs apply?
Schedule 2 of the Building Regs states that non-habitable buildings are exempt from the requirements of the building regs. That’s fine except it leaves an obvious grey area, being the definition of ‘habitable.’
One rule of thumb is that if the new structure is outside the ‘heated envelope’ then it is regarded as non-habitable. Thus a porch constructed outside the front door would not be deemed to be habitable, nor a ‘bolt-on’ style conservatory, and neither would require building regs. However, if you take the connecting doors off, then the new space is deemed to be habitable. As such, the new structures have to meet all the building reg requirements: i.e. foundations have to be passed, structural stability must be checked, insulation and ventilation must meet regs.
Certain internal works also require building regs approval:
• removing load-bearing walls
• forming a new bathroom or cloakroom
• replacement windows
• replacing boilers
• loft conversions
• major electrical work and all electrical work to kitchens and bathrooms
Most local authorities keep records of building regs approvals going back around 15 years. If you undertake relevant work on your home without building regs approval, you may not be called to account until you come to sell the house when the lack of building regs may come to light.
One rule of thumb is that if the new structure is outside the ‘heated envelope’ then it is regarded as non-habitable. Thus a porch constructed outside the front door would not be deemed to be habitable, nor a ‘bolt-on’ style conservatory, and neither would require building regs. However, if you take the connecting doors off, then the new space is deemed to be habitable. As such, the new structures have to meet all the building reg requirements: i.e. foundations have to be passed, structural stability must be checked, insulation and ventilation must meet regs.
Certain internal works also require building regs approval:
• removing load-bearing walls
• forming a new bathroom or cloakroom
• replacement windows
• replacing boilers
• loft conversions
• major electrical work and all electrical work to kitchens and bathrooms
Most local authorities keep records of building regs approvals going back around 15 years. If you undertake relevant work on your home without building regs approval, you may not be called to account until you come to sell the house when the lack of building regs may come to light.
14 Sept 2005
The shit misses the fan
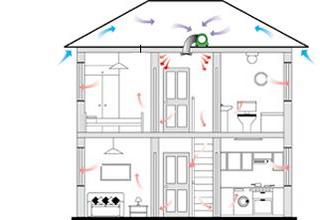
I'm considering installing a positivive input ventilation system like Nuaire’s Drimaster 2000? Any feedback?
Mark reckons:
Of all the varieties of ventilation systems you can fix into a building, this one has to be the worst.
Despite the rumours, positive input ventilation (PIV) like Nuaire's Drimaster (diagram above) probably won't be overlooked by the revised Part F of the E&W building regs, if only because there are a number of cases where it has been shown to work well. Usually these are on social housing schemes with condensation problems.
However, a new(ish) well-insulated house really shouldn't suffer from condensation problems. At normal relative humidity levels, the dew point is down at around 12°C and condensation won't occur at temps above this. So in this respect, it's answering a non-existent problem.
The only place where the temperature may fall below 12°C is within the roof or the external walls, so it's a good building principle to not encourage internal, moist air into these spaces. Which is exactly what PIV does.
The other major quibble with these single outlet fans (and this goes for the negative pressure fans as well) is that with just one inlet/outlet point, there is ridiculously little control over just where the air is blown or drawn from. Although the diagrams show the air gently wafting all through the house, in reality it's going to take the path of least resistance, which may be straight to or from the nearest trickle vent or badly-fitted window. The larger the house, the worse this effect will be: expect 90% of the house to remain completely unventilated.
Just compare this crude device with the heater/cooler in your car where you frequently have up to six outlets, some of them directional. I think the standard set-up of trickle vents and the odd extractor fan is preferable: they give you more control and are much more adaptable.
13 Sept 2005
Jan Kaplicky: Architect, Snob

The latest to stick his head above the taste parapet is Jan Kaplicky, head of Future Systems, who are best known for the media centre at Lord’s cricket ground, otherwise known as “ET’s head”. Whilst his designs may be white-hot contemporary, his social attitudes sound like they have been lifted straight from "The Importance of Being Earnest."
Here’s what Kaplicky thinks of Britain in the 21st century (writing in The Quarterly, Autumn 2005)
• “We can’t endlessly convert Victorian properties, it leads nowhere.”
• “Look at the rubbish you see on the train an hour from London: the land can’t be trashed with little boxes again and again.”
• “Who cares what dull repeats grace the hangers of M&S, when Armani and Galliano are creating cutting-edge designs.”
The stuff Kaplicky designs is fun, in an oh-so-clever, post-modern way. It’s also amazingly expensive and needs very wealthy clients to commission it. As such, I have no problems with it. I have seen his “House for a Wealthy Labour MP in Pembrokeshire” — pictured here and if you walk the Pembrokeshire coast path between Broadhaven and Nolton, or simply drive along the coast road, you can hardly miss it — and it’s truly an amazing site, especially in comparison to the very unprepossessing timber-clad shacks which are its neighbours. The locals refer to it as “The Teletubby House”: they can see the funny side of it.
Not so, Kaplicky. Just why does he have to be so pompous? I don’t hear classical musicians moaning about how awful pop music is, or poets complaining that the Sun is terribly badly written. If Kaplicky chooses to wear an Armani dressing gown in his multi-coloured greenhouse, good luck to him, but must he put down everyone who shops at M&S and lives in a “dreary box within an hour from London.” That just happens to be about 15 million people. I have no doubt that a couple of million of them, at least, would jump at the chance of living in a Future Systems house, but there are probably only a couple of hundred who could afford to. Maybe that’s Kaplicky’s real beef.
9 Sept 2005
On prices in the Housebuilder's Bible

Firstly, can I congratulate you on a fantastic book for anyone who wants to understand the options when building or just improving a property. I have found your book invaluable for grasping what is technically required for a multitude of projects on my house, in order to organise any kind of contractor or even DIY work.
I have the 2002 edition of The Housebuilder's Bible and do however have a concern about general pricing. I have pretty much read your book cover to cover and have always thought that your price estimates looked very optimistic based on any quotes I've ever had from any contractors. I do try to allow for the fact that I live on the South Coast (Hampshire) and there has been quite a lot of increase in labour rates in the last 3 years, but even with this considered, I can't get estimates from any contractor even close to your tables.
A specific example is that you estimate 8 hours / £200 for a plumber to install a boiler, and 4 hours to install a cylinder. Even then, you state £25 per hour is probably too HIGH, but allows for a typical mark-up on the supplied units. I have just been quoted £3300 and £3500 by 2 plumbing firms to replace my boiler and replace my copper cylinder with a Mains pressure system. There is no primary pipework to run, just the local connection pipework to adapt, and the boiler isn't moving location so the flue vent is already there. I know I can buy the boiler (Potterton 24KW), Cylinder (Megaflo 210ltr) + flue kit for £1700 inc., so that means they're making at least £1600!!! I can't see the job taking more than 2 days, (probably more like 12 hours) including removing the old units. That says they are making £100 to £135 per hour! That's up to 5x your "generous" £25 per hour.
Other smaller plumbing job quotes also seem to reflect this ridiculous labour rate, so am I in the wrong job or am I just picking outlandishly greedy plumbers?
I've also had various quotes over the last 2 years quotes for UPVC DG, and general building work, which come in at anything from 3x your reckoning in the Bible, upwards. When I have questioned pricing, no contractor has ever agreed to reduce the price, usually insisting they'd be making a loss if they reduced it. How can a 3m stud wall with a door fitted cost £1000? !!
I notice the property developer and self-build programs on TV, and
magazines like "Build it" all quote success stories from people who "built a £300K house for £80K" or "completely renovated, extended and loft converted for £40K". I wouldn't even get close to this price for the amount of work involved in these projects based on the estimates I get.
Why is there such a disparity? Is South-East really that far out with the averages you seem to work from? Would it have something to do with me having a big house and therefore any contractor thinks we're "loaded" and therefore we won't flinch at these stupid prices?
Let me know your thoughts. Perhaps there is a formal study of the pricing in the building contractor industry across the country that can help answer my questions?
Still a great book though and better than anything else out there! Can't help think there's room for a bigger section on evaluating how "reasonable" a quote is and maybe a rolling addendum specifically to adjust prices for different areas, kept up to date.
Best Regards,
Matt Latter
Mark replies:
Thanks for the warm comments, Matt. As to your concerns, it's difficult to comment on individual quotations as I don't know the extent of the works but it does look as though your are ignoring the whole issue of the contractor's mark-up, which gets progressively larger as the job gets smaller. My labour and materials prices in the books are just that, labour and materials, and should not really be used to work out quotations. On small refurb jobs, in particular, it's quite usual for contractors to add on 50% to labour and materials to cover the "hassle factor." There may be things in the way, access may not be easy, there may be all kinds of extra work to undertake, the installation may not work as planned from day one, there are guarantees and call backs to factor in, plus the overheads of running small businesses which are significant. These are deliberately ignored in the costings in the Bible, which looks at how much it should cost to build a house, not what you would be charged for having that work carried out by a builder.
For instance, earlier this year, I replaced an ancient and knackered mains-pressure cylinder with a new 210lt Megaflo. The plumber took the best part of a day to get the new Megaflo in (there was carpentry work involved in adapting the airing cupboard), but he also took nearly four hours getting the old one out (draining down the system, adjusting the pipework). Plus he had (and needed) a mate. So when I say that a Megaflo can be put in in 4 hours (it's actually gone to 6 in the new book), it can, be but it can also take much longer.
> I notice the property developer and self-build programs on TV, and
> magazines like "Build it" all quote success stories from people who "built
> a £300K house for £80K" or "completely renovated, extended and loft
> converted for £40K". I wouldn't even get close to this price for the amount of work involved in these projects based on the estimates I get.
> Why is there such a disparity?
A combination of poor maths and ignoring soaring land prices during the duration of the job.
> Is South-East really that far out with the
> averages you seem to work from?
No. It's maybe 20% more expensive on labour rates; materials are the same nationwide.
>Would it have something to do with me
> having a big house and therefore any contractor thinks we're "loaded" and
> therefore we won't flinch at these stupid prices?
No, I don't think so, though it's surprising how many people think this. If you have got a lot of work, then perhaps you should consider hiring guys on a cost plus basis. You effectively take the risk on your own shoulders if things go wrong. The rates should be dramatically cheaper but you will find yourself in one or two contractual knots when people make cock-ups (they will) and you have to pay them twice for doing the job they should have done right first time around but didn't. Once you go to fixed price quotations, on small jobs, the price rockets. This doesn't make the tradesmen greedy; it's simply a realistic assessment of the risks taken on in giving fixed price quotations.
Avoiding drain smells in the bathroom
Anthony Cam asks:
I have used an air admittance valve on my soil stack which has worked fine for the three months since we moved in but we now seem to have smells emanating from the wet floor drain in the shower/toilet and, more recently, from the washbasin in the bathroom. Would an open-vented stack fix this?
Mark reckons:
The probable cause of your problem is the failure of the water traps in your shower and your basin. However, it's difficult to pinpoint the precise reason for this as there are several causes of trap failure.
The commonest one is due to something called 'induced siphonage': this occurs when the water in the traps gets sucked down the waste pipes by pressure created by stuff happening elsewhere in the waste system.
Why should this happen in some systems and not in others?
There are a number of identified causes: the waste pipes maybe the wrong size for the appliance, or the individual runs are the wrong length or laid at the wrong fall, or the jointing with the soil stack may be too close to other connections. The best practice notes for what should happen, in an ideal world, in order to avoid these problems are all set out in Part H1 of the E&W building regs, but these are often ignored (they rarely get inspected) and are sometimes just impractical to install in any event.
If the water traps fail, then there is an obvious risk that drain smells will waft up into the bathroom. The vented soil stack is a designed as a failsafe in event of the water traps failing: the bad smells will usually take the route of least resistance, being straight up the stack and out through the roof. An air admittance valve (AAV), used more and more widely these days in place of vented soil stacks, does not provide nearly such a good escape path for bad smells; they only open when there is a significant pressure imbalance between the waste pipes and the surrounding house. If your waste traps have failed, the bad smells will be far more likely to seep out through your plugholes than through your AAV, as your traps have now become open pathways for the foul air.
What to do about it? One potential solution might be to replace the AAV sitting at the top of your stack with a full height, open-vented stack, exiting through the roof: it might just do the trick, but it might not. If that doesn't sort it, then you then have to re-plumb the waste runs.
If you do, then consider replacing the existing traps with Hepworth HepVO valves (pictured adjacent, pronounced Hep Vee-Oh), a patented non-return valve which has been on the market since 1997. The HepVO valve system is engagingly simple to understand. There are only three components; the valve itself which looks pretty much like any other piece of pushfit plastic pipe fitting, a straight connector and a knuckle or bend, each available in two sizes (32mmm for basins, 40mm for baths). The innovation is inside the valve where a one-way membrane is stretched across the walls: this allows water and air to pass through it downstream into the waste pipes but stops foul air passing upstream into the house. They are widely available from plumber's merchants (though they sell remarkably few, it seems) at a cost of between £12 and £15 a time.
Earlier this year, the BRE (Building Research Establishment, the UK's premier building research body) published an assessment* of the product. It was remarkably positive about the valve in almost all applications you could think of using it but one conclusion was particularly interesting: it suggested that when you use two or more HepVO valves in a top floor bathroom, you no longer require either an open-vented soil stack or an AAV stub-stack arrangement.
So if you can get access to the traps that are defective, I would have thought replacing them with HepVO valves would be a very good move.
* 'Self-sealing waste valves for domestic use: an assessment BRE Paper IP5/05 by White, Griggs and Sutcliffe.' This paper is also of interest in that it highlights ten causes of water trap failure being:
• self siphonage
• induced siphonage
• compression or positive pressure
• evaporation
• wind effect (aka wavering out)
• foaming
• momentum
• capilliary action
• leaks
• movement (boats and caravans only, or possibly earthquakes)
Who would have thought the humble water trap could be so cursed!
I have used an air admittance valve on my soil stack which has worked fine for the three months since we moved in but we now seem to have smells emanating from the wet floor drain in the shower/toilet and, more recently, from the washbasin in the bathroom. Would an open-vented stack fix this?
Mark reckons:
The probable cause of your problem is the failure of the water traps in your shower and your basin. However, it's difficult to pinpoint the precise reason for this as there are several causes of trap failure.
The commonest one is due to something called 'induced siphonage': this occurs when the water in the traps gets sucked down the waste pipes by pressure created by stuff happening elsewhere in the waste system.
Why should this happen in some systems and not in others?
There are a number of identified causes: the waste pipes maybe the wrong size for the appliance, or the individual runs are the wrong length or laid at the wrong fall, or the jointing with the soil stack may be too close to other connections. The best practice notes for what should happen, in an ideal world, in order to avoid these problems are all set out in Part H1 of the E&W building regs, but these are often ignored (they rarely get inspected) and are sometimes just impractical to install in any event.
If the water traps fail, then there is an obvious risk that drain smells will waft up into the bathroom. The vented soil stack is a designed as a failsafe in event of the water traps failing: the bad smells will usually take the route of least resistance, being straight up the stack and out through the roof. An air admittance valve (AAV), used more and more widely these days in place of vented soil stacks, does not provide nearly such a good escape path for bad smells; they only open when there is a significant pressure imbalance between the waste pipes and the surrounding house. If your waste traps have failed, the bad smells will be far more likely to seep out through your plugholes than through your AAV, as your traps have now become open pathways for the foul air.
What to do about it? One potential solution might be to replace the AAV sitting at the top of your stack with a full height, open-vented stack, exiting through the roof: it might just do the trick, but it might not. If that doesn't sort it, then you then have to re-plumb the waste runs.

Earlier this year, the BRE (Building Research Establishment, the UK's premier building research body) published an assessment* of the product. It was remarkably positive about the valve in almost all applications you could think of using it but one conclusion was particularly interesting: it suggested that when you use two or more HepVO valves in a top floor bathroom, you no longer require either an open-vented soil stack or an AAV stub-stack arrangement.
So if you can get access to the traps that are defective, I would have thought replacing them with HepVO valves would be a very good move.
* 'Self-sealing waste valves for domestic use: an assessment BRE Paper IP5/05 by White, Griggs and Sutcliffe.' This paper is also of interest in that it highlights ten causes of water trap failure being:
• self siphonage
• induced siphonage
• compression or positive pressure
• evaporation
• wind effect (aka wavering out)
• foaming
• momentum
• capilliary action
• leaks
• movement (boats and caravans only, or possibly earthquakes)
Who would have thought the humble water trap could be so cursed!
6 Sept 2005
Taking trees down slowly
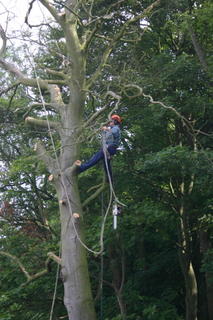
What the hell does it cost to fell a beech tree? Tony had three quotes, which ranged from £500 to £800 plus VAT and excluding any value that the timber might have, which goes to the fellers as well. If it could be felled, lumberjack-style, with cries all around of “Timber,” it would be quite a bit less, but because of its position it has to come down bit by bit. Touch wood.
Although the main stump is good and straight, it’s all set to be turned into nothing more interesting than firewood. I asked Tony, who is a skilled woodworker, whether he didn’t fancy a beech worktop or two, but he wasn’t moved. “Don’t like beech, it’s very dull.” So firewood it is.
The tree surgeon, Paul Batram, from Ipswich, appeared with his mate and a large shredder around 9.am this morning. They had finished by 2.30pm. In between times, he had swung around in the branches doing a passable imitation of Tarzan, only wielding a chainsaw. It was an awesome site. Each section-to-be-cut was first roped up, then cut, then directed down to the ground by the mate wielding the rope. Gradually, Paul worked his way up to the very top and then he began to take down great chunks of the stump from above his head. By now it was getting a little hairy just watching this from across the road, wondering how he was going to achieve all this without killing himself. As he worked down the main stump, his mate on the ground played an ever more crucial role, ensuring the falling sections didn’t take Paul down with them. The last few sections were actually pulled down with ropes from the ground, using their pick-up truck, Paul having first sawn through 95% of the trunk from a ladder.
I spoke to Paul whilst they were clearing up and he said that he had been doing this since 1967 — he must be at least 60 by now, but is lithe as a cat and must be fitter than many men half his age. “I’ve had a couple of falls, mind, which aren’t too clever, but this game certainly keeps you fit.”
If you ever need a tree lopping or taking down and it’s in a difficult spot, I really don’t think you could do better than this guy. He works all over East Anglia and even down into London, though “as infrequently as possible.”
If you ever fancy moving a tree, rather than cutting it down, there is a business called Practicality Brown, based in Oxfordshire, that specialises in this. They hire tree spade machines by the day. A 1100mm diameter machine moves trees with max diameter 10% of spade size (e.g. 110mm) and costs c. £750 for a day’s hire, according to location of work. The average number of trees moved per day would be 15 and guying and feeding each tree costs around £50, therefore the cost of moving 15 x 100mm diameter trees is around £100 +vat each. They have a larger tree spade to move trees up to 160mm diameter, costing an average of £170 each, based on 15 trees. Trees above 160mm diameter can be moved by crane, with costs starting at £2000 each - yes, the costs increase dramatically with tree size.
Contacts
East Anglian Tree Surgeon: Paul Batram 07742 221184
Alastair Beddall
Practicality Brown Ltd
Direct Tel: 01295 690011
Mobile: 07836 732200
email: abeddall@pracbrown.co.uk
5 Sept 2005
How to build on a floodplain
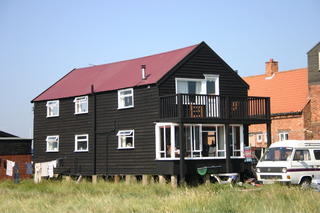
Never mind. I think I may have some help to proffer. 80 miles up the East coast, at the mouth of the Blyth Estuary in Suffolk, lies the artists-colony-cum-crabbing-centre that is Walberswick. It’s a beautiful spot and well worth a day out, if you are ever in the area. Incidentally, it is home to many fine properties that have been taken down and moved here from other parts of the country, so it’s already a global leader in the practice of off-site manufacturing.
I have been visiting Walberswick for the best part of thirty years and have oft looked at, with a slight feeling of envy, the two timber-clad beach houses, sandwiched between the car park and the River Blyth. They are just sheds, really, but two very cool sheds. I can sort of picture myself living in one of these, wearing not much more than a fisherman’s smock, a beard and a big smile.
But I must admit that, until this weekend, I had never noticed that they are both built on stilts, presumably to keep them up above the spring tides that must from time to time swamp the car park and the salt marshes behind. Stilts! Just the thing for the Thames Gateway Sustainable Communities, or whatever they are currently known as. I reckon a good bunch of chippies could knock one of those up in less than a month and have enough change from £60k for a month on the Costas. Or, being Walberswick, maybe six months in Goa.
Can we speed up the planning process?
Sara writes:
Our plans are ready to go in and have been drawn up by a local bloke who has been very good but a bit slow (because he is always busy). We choose him because we have used him before, he knows the process and the planners.
He has done the plans for a fixed price and will charge us around £200 to "put the application in and manage it to decision". We want him to do that as we may have some neighbour issues and can therefore play good-cop, bad-cop! Concern is he doesn't have the same incentive as us to get it approved so I'm thinking we should offer him a £500 bonus if the application is approved and to speed it up an extra £500 if it is approved before Christmas ?
Anyone done anything like this? Any reason not to?
Mark reckons:
The nub of the problem here is that 80% or 90% of the delays in planning are caused by the planners themselves. Your man could be very "on the ball" but still not get a result before Xmas, through no fault of his own. Also you mention there are "issues with neighbours": it may be that the whole process becomes complex and convoluted and an early decision may not be welcome because it may well be a refusal!
Coincidentally, I just absorbed this snippet, extracted from Housebuilder magazine (Sep 2005).
Developers are increasingly being forced onto a "reject and resubmit" planning merry-go-round in order to win planning approval, as planning authorities seek to meet the government's speed-of-decision targets. Research published by Housing Market Intelligence reveals that the government's service delivery targets for planning authorities, which encourages them to determine 60% of major residential and industrial applications within 13 weeks, have not led to an improvement in the planning process, as the government has claimed. Planning authorities are now far quicker to reject applications, leading applicants to resubmit projects rather than entering into negotiations. This approach shortens decision times, on which authorities are targeted, but there is little evidence to suggest that it is reducing the time taken to get projects through the planning process. In SE England, currently a third of all projects granted planning permission have been rejected at least once (compared to just 19% only three years ago) and in London as many as 1 in 10 projects have required at least three applications before approval is granted.
Our plans are ready to go in and have been drawn up by a local bloke who has been very good but a bit slow (because he is always busy). We choose him because we have used him before, he knows the process and the planners.
He has done the plans for a fixed price and will charge us around £200 to "put the application in and manage it to decision". We want him to do that as we may have some neighbour issues and can therefore play good-cop, bad-cop! Concern is he doesn't have the same incentive as us to get it approved so I'm thinking we should offer him a £500 bonus if the application is approved and to speed it up an extra £500 if it is approved before Christmas ?
Anyone done anything like this? Any reason not to?
Mark reckons:
The nub of the problem here is that 80% or 90% of the delays in planning are caused by the planners themselves. Your man could be very "on the ball" but still not get a result before Xmas, through no fault of his own. Also you mention there are "issues with neighbours": it may be that the whole process becomes complex and convoluted and an early decision may not be welcome because it may well be a refusal!
Coincidentally, I just absorbed this snippet, extracted from Housebuilder magazine (Sep 2005).
Developers are increasingly being forced onto a "reject and resubmit" planning merry-go-round in order to win planning approval, as planning authorities seek to meet the government's speed-of-decision targets. Research published by Housing Market Intelligence reveals that the government's service delivery targets for planning authorities, which encourages them to determine 60% of major residential and industrial applications within 13 weeks, have not led to an improvement in the planning process, as the government has claimed. Planning authorities are now far quicker to reject applications, leading applicants to resubmit projects rather than entering into negotiations. This approach shortens decision times, on which authorities are targeted, but there is little evidence to suggest that it is reducing the time taken to get projects through the planning process. In SE England, currently a third of all projects granted planning permission have been rejected at least once (compared to just 19% only three years ago) and in London as many as 1 in 10 projects have required at least three applications before approval is granted.
3 Sept 2005
Hardwood floors — the true costs
The job was undertaken by a local business called The Traditional Flooring Co, based in Gt Eversden near Cambridge, who had, earlier in the year, installed some Marmoleum for us in a bathroom refit. The job was arranged in February, and the holiday booked at the same time, so that the whole thing could be undertaken as seamlessly as possible. Steve Jones, the proprietor, was as good as his word and he and his crew turned up at 9am on the Tuesday morning of our departure, and we left for the airport an hour later, having removed the sofas and the Welsh dresser. On our return from Crete, a week later, the job was finished and the floor looked absolutely stunning, having been given three coats of Bona Kemi Traffic, a two part water borne polyurethane floor lacquer “for areas subject to extremely high usage where a very matt or near invisible finish is required.”
I must admit that when I agreed the quotation six months ago, I didn’t pay much attention to the amount. I was, frankly, just delighted to be able to get the job done when we weren’t in the house. Now that I am about to write a cheque out, it suddenly dawns on me what an enormously expensive operation it’s been.
The bill, including VAT, is £1968. The area sanded and sealed is around 75m2, give or take the odd kitchen cabinet, so that translates as just over £25 per m2. My first thought is “that’s outrageous, you can install a new floor for less than that.” But subsequent thoughts add a little realism. Although it’s nominally 12 x 6 m area that’s being sanded, it’s subdivided into four rooms, each with numerous projections and indentations: i.e. it’s really fiddly. I can see that it would take at least 30 hours to sand this all down, most of it spent on the edge sanders – remember sanding is a three stage process in itself. Add in another 10 hours for the three coats of Bona Kemi, plus the cost of this as well as the sanders, and you can see that Steve’s quote doesn’t look so outrageous after all. It probably represents a 50% mark-up on his own costs: that sort of mark-up is worth paying for a job done well (it has been) and done on time (it was).
But it does make you realise just how much it costs to keep a hardwood floor looking good. I checked back to my records of how much this floor cost to install back in 1992. The French chestnut was bought from Petersens in Aylsham, Norfolk at cost just under £1500. I remember thinking I’d got a bargain, but back then I didn’t know about the reburb costs.
Trouble is we have dogs, two lovely but very hairy Retrievers, the younger one pictured on the newly sealed floor this very morning. When the ground turns muddy in a month or two, the sheen on the newly sealed floor will start to disappear very quickly…
The Traditional Flooring Company: 01223 264800
1 Sept 2005
Housebuilding on Crete

This summer we holidayed on Crete and I had the chance to renew my acquaintance with Greek building methods, as there was a new home under construction barely 200 metres from our villa at Istron Bay. How little things seem to have changed. The actual house was, or will be, a stunning addition to the coastline when it’s finished, but the building methods seem to be incredibly slow and disorganised. Maybe it was the August effect – it’s a bit hot to race around much in Crete in August — but even so, the pace of work was ridiculously slow. Just about the only progress of note that took place during our weeks stay was the top two metres of a chimney being built-up in clay blocks: this took a mason and a labourer about two hours, much of it spent shinning up and down a scaffold tower without a ladder in sight.
In fact the whole scaffolding/access arrangements were not just primitive but verging on the bizarre, to my eyes. Most of the scaffold was timber, built-into the walls and never more than two boards wide. It’s hard to see how anyone could work effectively off it, let alone safely. But I don’t think health and safety features very highly on Cretan building sites. Afterall, back in 1941, these guys’ grandfathers thought nothing of slitting the throats of German paratroopers as they fell from the sky: I don’t suppose their grandsons would be too impressed by risk assessments or method statements.
Subscribe to:
Posts (Atom)