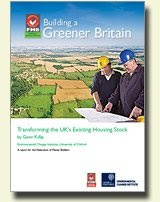
But times change. The FMB have sensed that the agenda may be moving away from the big plc housebuilders and towards the repair, maintenance and improvement (RMI) sector, which is what their core membership do. Sensing that there may well be a lot of work to be done in future-proofing our existing housing stock, they commissioned the Environmental Change Institute at Oxford to write a report called Building a Greener Britain and then put on a launch event earlier this month, the first time the FMB have ever been involved in such a thing. As well as a presentation by Gavin Killip, the impressive author of Building a Greener Britain, they managed to draw both the junior housing minister Iain Wright and the shadow housing minister Grant Shapps. For an organisation with no political track record, this was quite a coup.
I was going to write a report about the proceedings but got delayed by one thing and another, not least going on holiday to Greece. And anyway the meat in the sandwich is Gavin Killip’s report and it wasn’t until last week that I got around to reading it and I must admit I am impressed. It’s remarkably free from waffle and it fleshes out the thinking behind 18 recommendations for policy changes that are clearly laid out right on page 6. I won’t list them here — you can download them yourself — but you’d have to be a real nit-picker to want to argue with any of them.
The one that the FMB particularly like is No 6, the recommendation that the UK government cuts the VAT rate on RMI work to 5% from its current 17.5%. I didn’t realise that this had been trialled in the Isle of Man, as well as several other EU states, and it results in a higher tax take for the government because fewer jobs get done for cash. If the government wanted to “do something” about cowboy builders (they do) and they want to increase their tax take (they do), then this seems like a no brainer.
My one reservation about the proposals is that it makes out that eco-refurbishment is easy and that bringing about 60% or 80% carbon reductions from the existing stock is simple. Despite the best endeavours of Russell Smith of Parity Projects to show how it’s done, I remain to be convinced. In fact, I’ve been thinking about this a lot over the past month and it’s tending to make me a little depressed. There’s a low hanging fruit issue here: there are some actions that are simple and cost effective, and there are some homes where it makes sense to “do the works.” But to make really deep cuts in energy use across mainstream UK housing….that’s going to be a tough nut.